A new process to stabilize metals at the nano level has the potential to create faster, more efficient turbines, feasibly improving everything from war planes to dams to ship engines.
A team of researchers including scientists from Arizona State University created a process that resulted in a super-strong nanocrystalline alloy, which resists deformation over long-term use.
“This process is revolutionary,” said Kiran Solanki, an associate professor in the School for Engineering of Matter, Transport, and Energy (Ira A. Fulton Schools of Engineering), one of the paper’s co-authors.
For the past half century, researchers have been working to make stronger materials. An aircraft flies by its engine. To make an aircraft fly faster, the engine turbines need to spin faster, or to produce more revolutions per minute. Nanocrystalline alloys are super-strong, but when engines run fast and hot, eventually the metal becomes deformed over time, or “creeps.” But the new process results in an alloy that resists deformation.
The process, invented by Solanki and colleagues at the Army Research Laboratory and the University of North Texas, stabilized a copper alloy at a micro level.
“These materials can last in high temperatures,” Solanki said. “If they last longer, and the temperature is high, every increment improves the efficiency of the engine.”
Using the new process, operating temperatures can be increased, fuel efficiency boosted, and the machine’s carbon footprint reduced. While no one uses copper for load-bearing applications like aircraft, “this technology can apply to any other materials,” Solanki said. “Anything where you have a power conversion.”
Advances in materials nanotechnology — manipulating matter on an atomic or molecular scale — made the process possible.
“For the last 20 years they thought this would never work,” Solanki said.
According to the paper’s authors, published last week in the journal Nature, the rate at which creep occurred in the alloy was six to eight orders of magnitude lower than in most other nanocrystalline metals — a spectacular improvement in durability.
“Now the question is, can we take this process and apply it to other materials?” Solanki said.
Two members of Solanki’s lab team, postdoc Mehul Bhatia and doctoral candidate Mansa Rajagopalan, were corresponding authors on the paper.
Top photo courtesy of freeimages.com.
More Science and technology
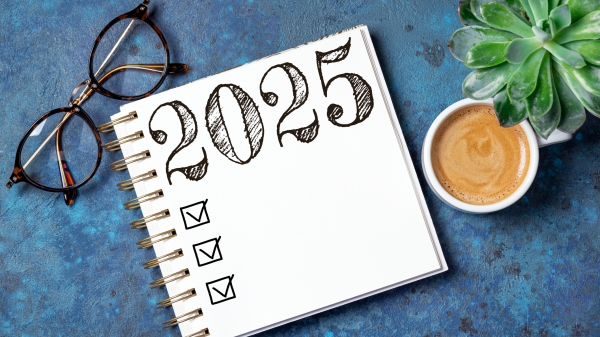
ASU professor shares the science behind making successful New Year's resolutions
Making New Year’s resolutions is easy. Executing them? Not so much.But what if we're going about it all wrong? Does real change take more than just making resolutions?Michelle Shiota thinks so. …
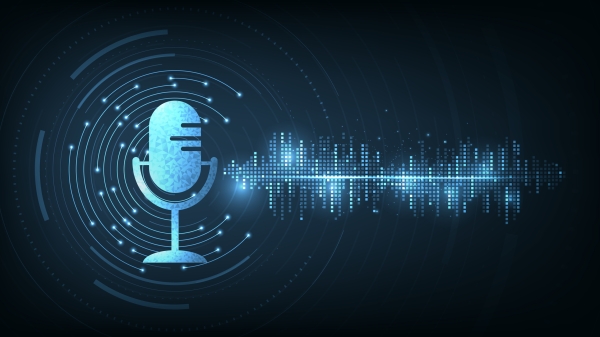
ASU student-run podcast shares personal stories from the lives of scientists
Everyone has a story.Some are inspirational. Others are cautionary. But most are narratives of a person’s path, sometimes a circuitous one, from one point in their lives to another.A new podcast…

The meteorite effect
By Bret HovellEditor's note: This story is featured in the winter 2025 issue of ASU Thrive.On Nov. 9, 1923, Harvey Nininger saw his future explode across the Kansas sky. He would become perhaps the…