Why chip manufacturers choose Arizona's desert environment

ASU Regents Professor Paul Westerhoff, the Fulton Chair of Environmental Engineering in the School of Sustainable Engineering and the Built Environment, part of the Ira A. Fulton Schools of Engineering at Arizona State University, and member of the Arizona Water Innovation Initiative at ASU. Courtesy photo
The true measure of a product’s success lies in its journey, from development to the environmental impact it leaves behind. In today’s climate, manufacturers are more committed than ever to finding the delicate balance between innovation and sustainability.
Semiconductor chip fabrication facilities, or fabs, are often called out for their high water consumption. At the same time, fabs are flocking to the arid Phoenix area.
To address their water use, fabs are seeking to develop net-zero water manufacturing facilities. The research, industry and municipal sectors in Arizona are making significant strides to achieve a water treatment engineering approach known as zero liquid discharge.
Using this approach, all water is recovered after manufacturing, and the residual salts plus chemical contaminants that remain are reduced to solids that can be safely disposed of.
ASU Regents Professor Paul Westerhoff, the Fulton Chair of Environmental Engineering in the School of Sustainable Engineering and the Built Environment (part of the Ira A. Fulton Schools of Engineering at Arizona State University) and member of the Arizona Water Innovation Initiative, explains how the semiconductor industry has established a strong presence in the Phoenix area. He notes that regions facing the greatest water challenges are also leading the way with innovative water conservation solutions.
Westerhoff explains why water usage and sustainability are so critical for this growing industry.
Question: Given Arizona’s dry climate and limited water resources, it’s surprising that such a water-intensive industry like chip manufacturing is thriving in the Phoenix area. What factors are attracting this industry to such a water-conscious region?
Answer: The dry climate and mindset toward water usage are Arizona’s biggest assets in many ways.
Beyond water, chip fabrication requires geologically stable ground, low humidity and a positive business climate for manufacturers and the families they employ. Even without Arizona’s approach to water usage, the dry climate is ideal.
Wherever you have the biggest water stresses is actually where communities see the biggest innovations in water conservation. Many companies have corporate environmental, social and governance, or ESG, goals for sustainability. Figuring out how to accomplish the water-related ESGs in Arizona takes real creativity.
You don’t see the same level of creativity related to water usage in Ohio or New York because we face a different reality here. We are now seeing innovative technologies first developed for chip manufacturing in Arizona are now being deployed nationally and even globally at other manufacturing facilities.
Q: What is the water treatment process for fabs? Why does it require such large amounts of water, and what makes it so costly?
A: Chip manufacturers buy tap water from their city just like regular people buy water to use in their homes. However, standard city tap water doesn’t meet the ultrapure requirements needed for semiconductor manufacturing.
While tap water is safe to drink, fabs must go a step further to remove all the salt and even the smallest particles of clay and other minerals before it can be used in the manufacturing process. On the other hand, drinking semiconductor ultrapure water would not be safe for humans because it is “too” clean and could remove essential nutrients from your body.
A typical chip may have 20 to 40 layers, and each layer needs ultrapure water to clean off particles, polymers or chemicals to get it ultrasmooth and ready for the next layer. Modern semiconductor chips have gaps of about four nanometers, so if you have even the smallest particle, it can get stuck and ruin the semiconductor.
Chips need extremely clean water, and they need a lot of it, so Arizona fabs and other nearby companies in the supply chain have been finding innovative ways to use the water for other processes.
Q: What happens to water after it is used, and how are companies working to offset their resource consumption?
A: Currently, fabs recover all the once-used water for chip manufacturing and treat it onsite. The purified manufacturing wastewater gets reused for other things, most often for temperature control in buildings and other parts of the manufacturing cycle.
Chip fabricators have not traditionally reused their wastewater as a source of ultrapure water for cleaning the layers, but globally now and in Arizona, we are conducting research to help de-risk this approach.
The most advanced industrial water-reuse research is coming out of the Arizona Water Innovation Initiative here at ASU. When proven successful, it will dramatically reduce the water footprint of fabs. The biggest impact comes from how fabs adapt their facilities to reuse their water, or even find new water and generate offsets within the watershed where manufacturing facilities are located.
In 10 years, you’re going to see the water footprint of these fabs decrease, and that’s being driven by the cities in which they are located. Fabs located in Arizona voluntarily do zero liquid discharge as strong local partners in our community. It costs them a lot more than all their competitors, but they do it to meet their corporate sustainability goals and because it is part of operating in the desert.
For many companies, manufacturing facilities located in Arizona are among their most water-efficient plants — despite or because we are in a most water-stressed location.
Q: Why are fabs reluctant to reuse their wastewater to make chips?
A: Fabs reuse as much water as possible for cooling and other parts of the manufacturing process. Traditionally, it has been more reliable for them to reuse that water in different ways than to use it to wash other chips in development.
However, the holy grail next step is to use reclaimed industrial water directly in chip manufacturing. Our team is working to measure specific types of chemicals that could pass through their industrial wastewater treatment steps, and if we detect them, what new treatment processes can be installed to destroy them.
We are also exploring other ideas, such as harvesting ultrapure water vapor from the air to make chips. We are helping to identify refinements to reduce the energy intensity of zero liquid discharge to help companies meet energy and greenhouse gas emissions standards that, in addition to water, are part of their environmental, social and governance goals.
The holy grail next step is to use reclaimed industrial water directly in chip manufacturing.
Paul WesterhoffASU Regents Professor
Q: How can the chip fab industry work to be more sustainable?
A: Direct reuse of water in a fab is the obvious focal point. Another big part of the footprint for chip manufacturers is the chemical supply chain and exploring uses for chemicals in their wastewater after making chips. Just like with water recycling, some fabs are expanding their efforts to recover and reuse chemicals.
For example, sulfuric acid is used in fabs and yields sulfate after being used. We can now recover sulfate from wastewater and recycle it to sulfuric acid again for onsite use.
Similar research is underway to recover and reuse organic solvents. Major national research is ongoing to find more environmentally benign chemicals that can be used in the manufacturing process. For example, PFAS, or “forever” chemicals, currently critical in chip manufacturing, but companies are looking for ways to replace them to ensure they don’t contaminate the environment.
Overall, we are seeing chip manufacturing evolve toward greener energy and improved reuse of chemicals.
Q: What barriers continue to exist within the push for sustainability and water usage?
A: Water is critical for all types of manufacturing, including chips. In most cities, 20% to 50% of the city’s “tap” water supports commercial, industrial and institutional water uses, and not just water in our homes. From fabs to hospitals, schools, hotels, airports, restaurants, beverage bottling and places we work, they all use water in different ways.
There is a real push to understand how these entities with nonresidential water uses can or should recycle water themselves.
Over time, you will see increasing focus not just on water conservation, but also on reuse at individual commercial, industrial and institutional facilities. These locations have a responsibility to balance reusing water with production and service goals, and potentially increased energy requirements, for onsite wastewater reuse. They will also need to train their staff on new tools.
It’s no small ask to get companies to change their procedures, but most realize their role in not only the economy but in operating in a desert where it is just common sense to be good water stewards.
More Science and technology

Stuck at the airport and we love it #not
Airports don’t bring out the best in people.Ten years ago, Ashwin Rajadesingan was traveling and had that thought. Today, he is an assistant professor at the University of Texas at Austin, but back…

ASU in position to accelerate collaboration between space, semiconductor industries
More than 200 academic, business and government leaders in the space industry converged in Tempe March 19–20 for the third annual Arizona Space Summit, a statewide effort designed to elevate…
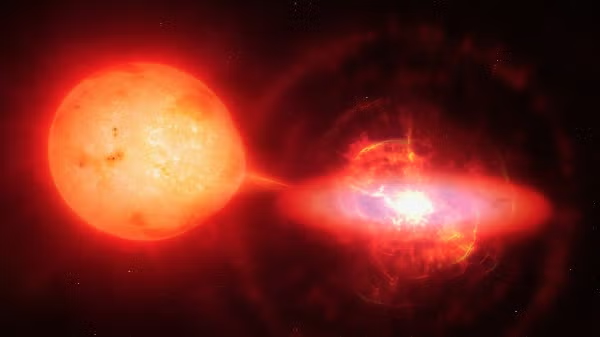
A spectacular celestial event: Nova explosion in Northern Crown constellation expected within 18 months
Within the next year to 18 months, stargazers around the world will witness a dazzling celestial event as a “new” star appears in the constellation Corona Borealis, also known as the Northern Crown.…