Defense contractor Raytheon had a $350,000 robot arm, used for smoothing the rough edges of metal, but it wasn't complete.
Raytheon turned to a team of Arizona State University students in the Ira A. Fulton Schools of Engineering.
In a dazzling feat of technical know-how and tireless dedication, the student engineers had the deburring robot up and running in 60 days. It dominated the students' schedules.
“I was either in class, here, or on the toilet,” said Jesse Wittkowski, who graduated this spring with a Bachelor of Science, Engineering in robotics and manufacturing.
The robot is huge. It’s like the Incredible Hulk’s arm, but made of orange metal. Together, the robot and the table it’s mounted on weigh 13,000 pounds — as much as an African bush elephant. The arm, which can hold 120 pounds and reach a little over 6 feet, machines parts to aerospace tolerances (think one-15,000th of an inch).
Raytheon shipped the robot from Tucson to the innovation lab on ASU's Polytechnic campus in Mesa. The industrial corporation chose to use the university's eProjects program, which brings students and industry together to solve real-world problems. Industry partners fund project expenses and receive full access to the results.
Video by Ken Fagan/ASU Now
“We had placed the robotic deburr project in storage at Raytheon after one of our suppliers could not complete development,” said Chad Spalt, a missile systems engineering fellow at Raytheon. “The ASU Polytechnic eProject program was an affordable way for us to continue technical development on the project, while building a stronger relationship with the ASU Polytechnic campus. The students solved a number of technical issues, and the robotic work cell will soon be slated for use in an industrial working environment.”
The robot arm was mounted in the top of the table, but it couldn’t reach everything. When the robot was lowered below the surface, it “thought” everything that was on the table was now in the table. The team had to figure out the mess. The challenge? Make it dance and get chips flying. At times it felt like starting from scratch might have been easier.
However, in life and engineering, “you’re not always starting on something from scratch,” said Rebecca Bell, who earned her BSEBachelor of Science, Engineering in robotics this spring. “We had a lot of debugging to do. It was diving in to see what the current state was and how to solve the problems.”
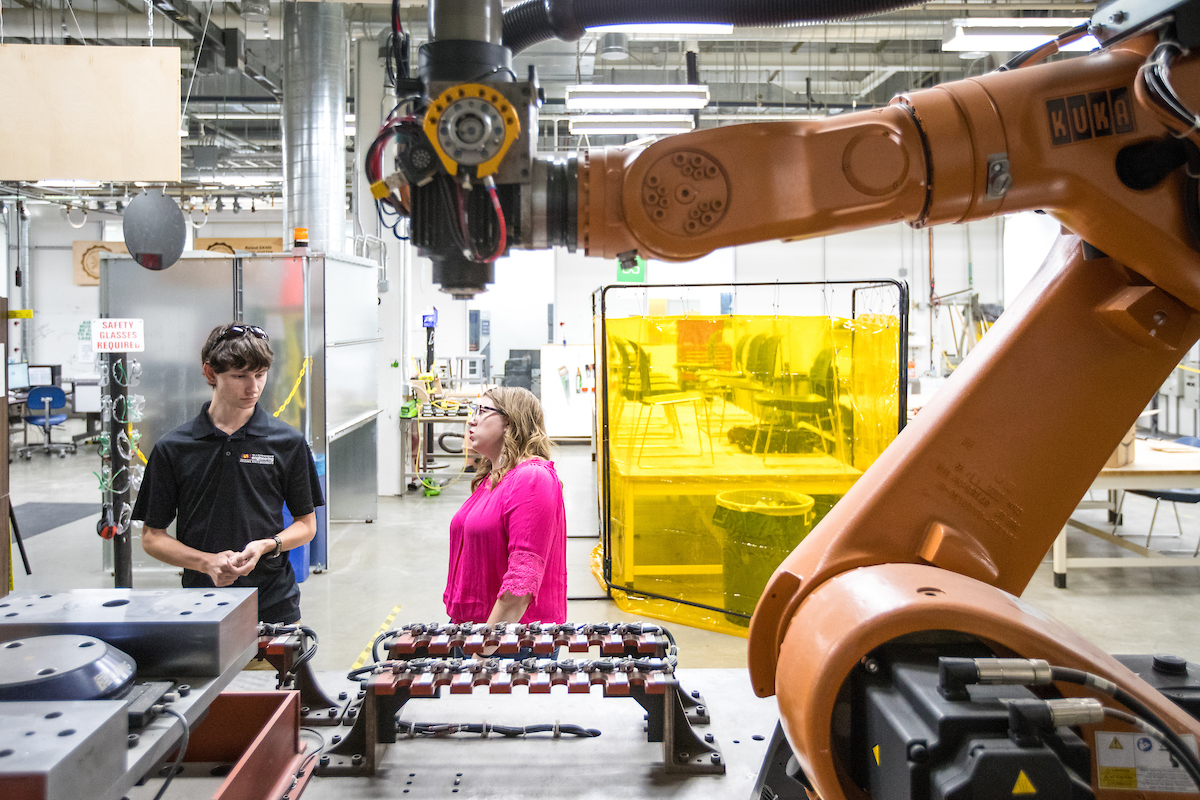
Recent engineering graduates Aaron Dolgin and Rebecca Bell talk about their work on the robotic arm at the Innovation Hub on the Polytechnic campus. Photo by Charlie Leight/ASU Now
And they were on their own, armed with everything they had just learned in four years.
“It was more the learning curve,” team leader Aaron Dolgin said. “No one at the university had used one of these.”
For Dolgin, his learning curve was managing the group. “It was being able to coach them through the waiting periods,” he said. “It was no small task.”
An internship at Northrop Grumman taught him a lot. (Dolgin now works there, after graduating last spring with a BSE in electrical engineering.)
“You’re bringing together multiple disciplines from engineering — management, global supply chain — and scheduling weekly industry partner meetings,” he said. “We kept them in the loop, and they kept us in the loop.”
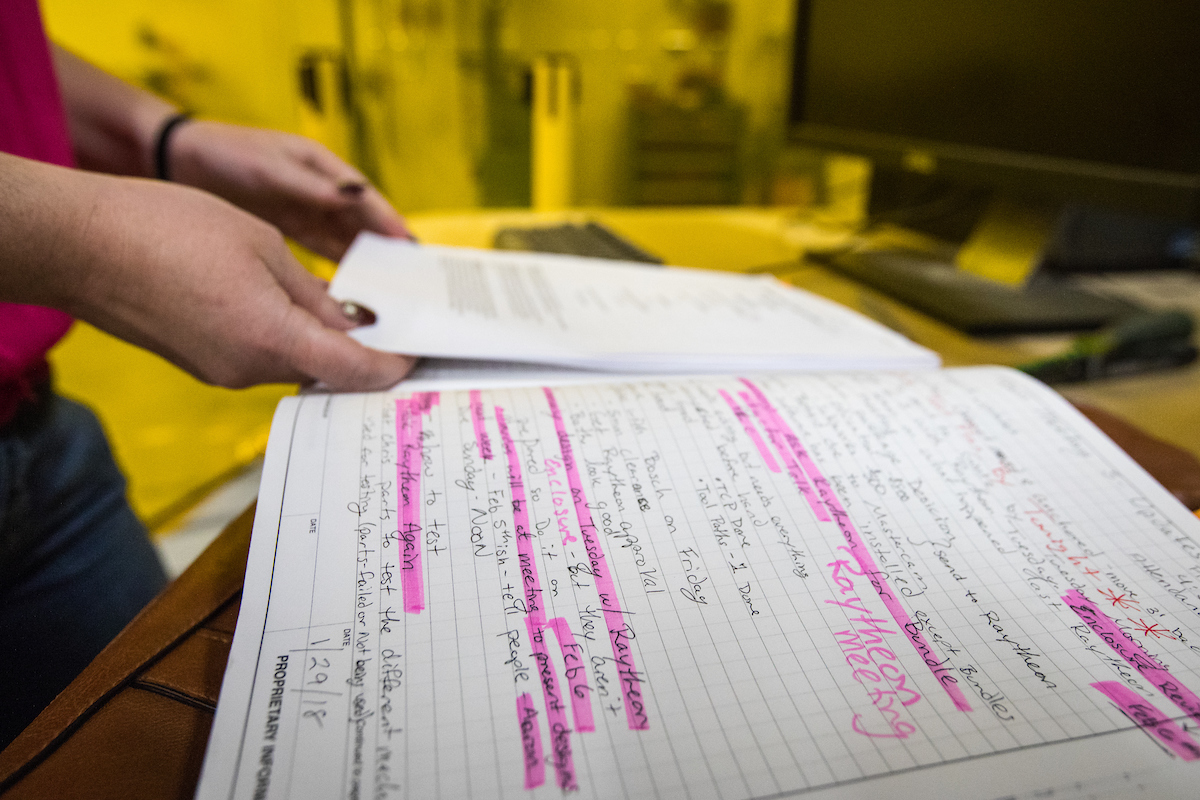
Recent robotics engineering graduate Rebecca Bell reviews her engineering notebook, called "The Bible" due to her meticulous notes on all meetings and all work done on the robotic arm. Photo by Charlie Leight/ASU Now
Riley Chicci had to check all the wiring and all the connections based on the schematics.
“There was a list as long as my arm of things I had to fix,” Chicci said.
Wittkowski had to teach the robot where its arm was in space.
“This was amazing,” he said. “I got to work with a real industrial robot.”
George Doucette was charged with liaising between the university and the corporation.
“It was just as much a project dealing with Raytheon and ASU as much as the robot,” he said. “I don’t mean that in a bad way. It was just getting an organization as big as Raytheon and an organization as big as ASU to meet in the middle was not easy.” Doucette graduated with a BSE in mechanical engineering systems.
“We may be the first capstone project to have middle management,” Chicci said. (Capstone projects are senior-year projects that require students to draw on everything they have learned. Chicci graduated with a BSE in robotics.)
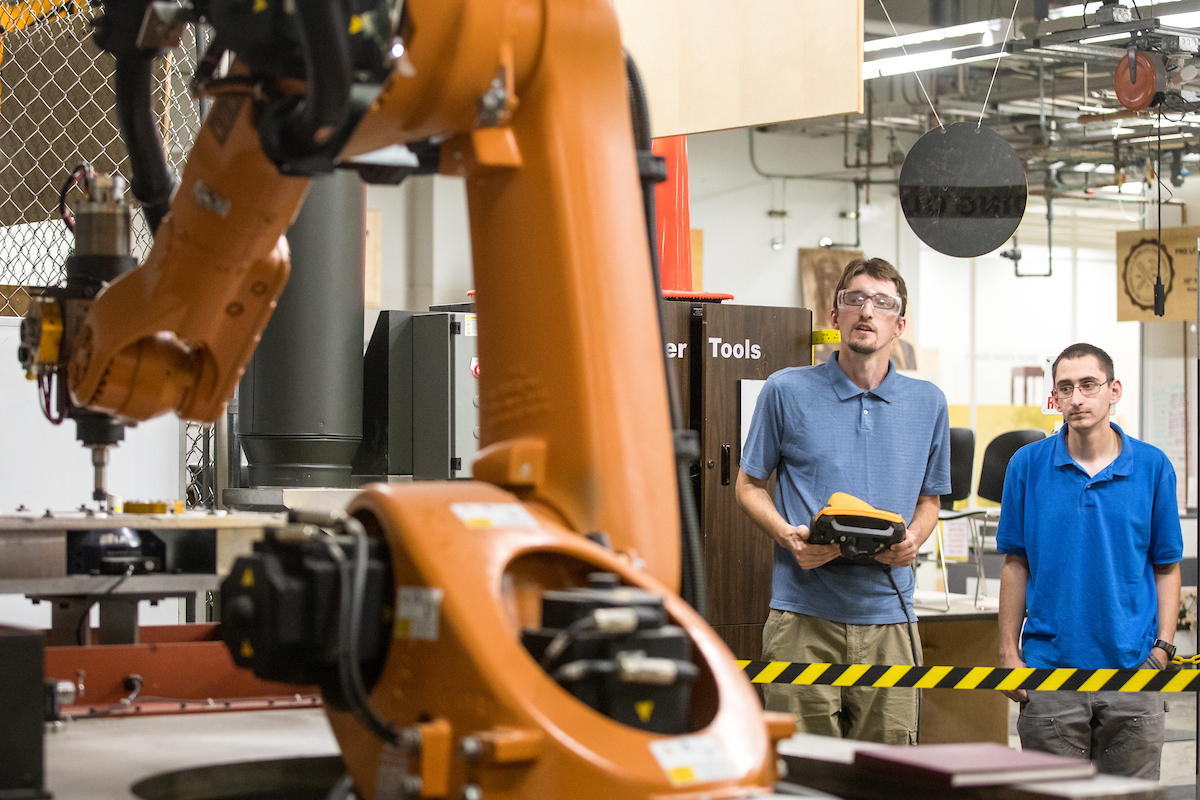
Recent robotics and manufacturing engineering graduates Jesse Wittkowski (left) and Riley Chicci watch the Kuka robotic arm perform functions. Photo by Charlie Leight/ASU Now
“They were really impressed because we found a lot of issues,” said Marcos Valenzuela, who graduated with a BSE in mechanical engineering.
The robot works at eye-blink speed when it’s throttled up. It’s actually a little eerie to see something so huge move so quickly, smoothly and precisely.
Raytheon couldn’t have been more pleased.
“We plan to continue working with the ASU Poly campus to refine their manufacturing engineering curriculum and better prepare their manufacturing engineering graduates to immediately contribute when they enter the professional workforce, perhaps at Raytheon,” Spalt said.
Top photo: The robotic arm goes through its paces at the Innovation Hub on ASU's Polytechnic campus on May 17. Raytheon delivered the nonworking deburring robot to ASU in hopes that it could reprogram the device after the former integration company failed. In the 60-day time frame, engineering students were able to program, run and test the massive arm. Photo by Charlie Leight/ASU Now
More Science and technology
Statewide initiative to speed transfer of ASU lab research to marketplace
A new initiative will help speed the time it takes for groundbreaking biomedical research at Arizona’s three public universities to be transformed into devices, drugs and therapies that help people.…
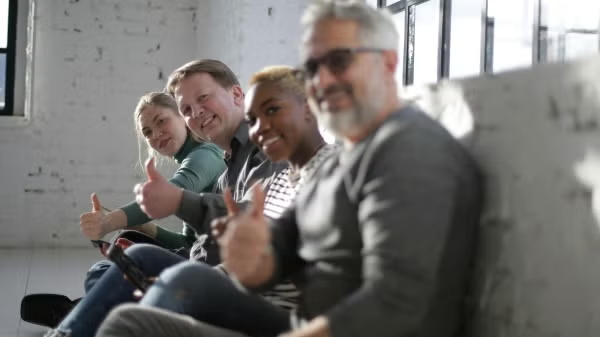
ASU research seeks solutions to challenges faced by middle-aged adults
Adults in midlife comprise a large percentage of the country’s population — 24 percent of Arizonans are between 45 and 65 years old — and they also make up the majority of the American workforce…

ASU research helps prevent substance abuse, mental health problems and more
Smoking rates among teenagers today are much lower than they were a generation ago, decreasing from 36% in the late 1990s to 9% today. The rates of alcohol consumption among underage drinkers…