Energizing the future of electric vehicle transportation
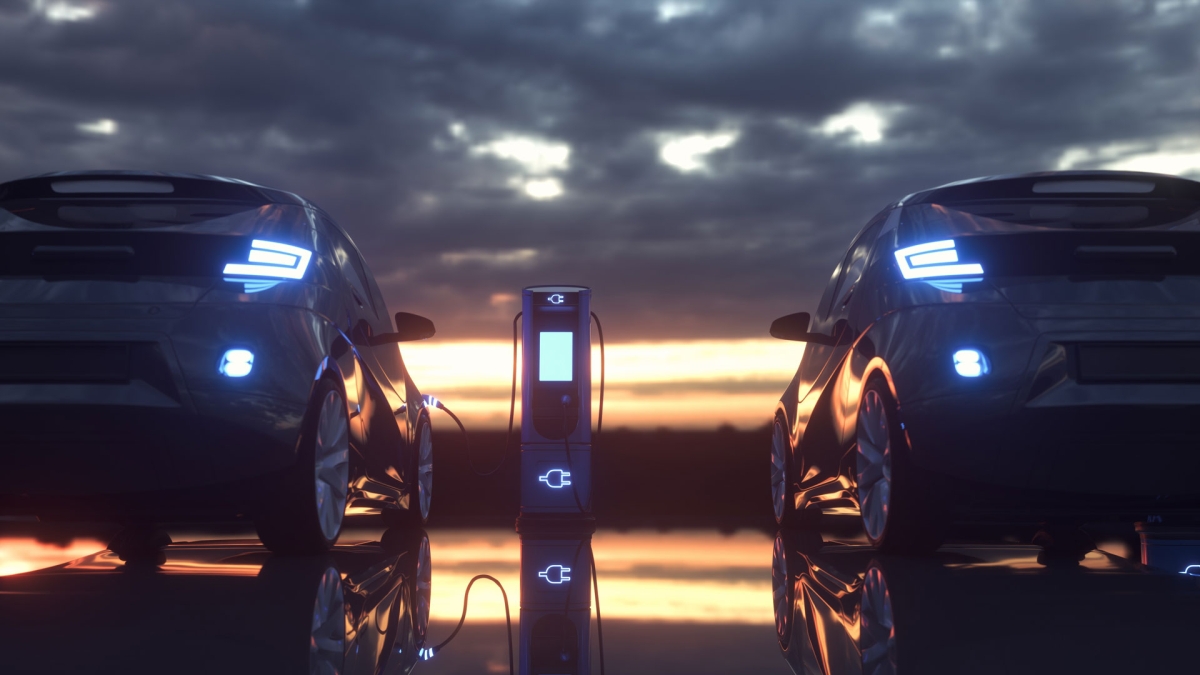
Electric cars charge in the evening. Xiangyang Dong, an associate professor of manufacturing engineering in the Ira A. Fulton Schools of Engineering at Arizona State University, received a 2024 National Science Foundation Faculty Early Career Development Program (CAREER) Award to investigate the use of 3D printing to build electric vehicle batteries. iStock photo
You've likely seen them whirring down the streets — electric vehicles, or EVs, are becoming more popular as the world shifts to climate-friendly transportation alternatives.
The U.S. Department of Energy has found that EVs combat the climate crisis by mitigating greenhouse gas emissions and improving air quality, resulting in a reduction in pollution-related health concerns. However, the rechargeable batteries used in EVs — essential components in the transition from the use of internal combustion engines in vehicles — come with some challenges.
School of Manufacturing Systems and Networks, part of the Ira A. Fulton Schools of Engineering at Arizona State University, says due to current barriers — such as charging infrastructure — heightened performance and energy efficiency will be essential to solidify the widespread adoption of electric vehicle transportation.
Existing research focuses on enhancing the chemistry and energy density of rechargeable batteries’ individual cells. Improvements to the protective mechanical battery enclosures, which reduce vehicles’ overall efficiency, have yet to be fully developed.
For his work to improve battery designs, Dong has received a 2024 National Science Foundation Faculty Early Career Development Program (CAREER) Award. His approach will explore the use of continuous carbon fiber-reinforced composites to create a new material that can support heavy structural loads while successfully storing electrical energy. The materials that make up the structure of vehicles’ bodies will, in and of themselves, serve as the vehicles’ batteries, resulting in a decrease in mass and volume and an increase in energy storage efficiency.
With more than the $600,000 in project funding, Dong will use a bottom-up strategy to transform continuous carbon fibers into 3D structural batteries, allowing for a variety of uses.
“The key here is to achieve high surface contact area and bonding between single carbon fiber and cathode materials within 3D structural batteries,” Dong says.
The new manufacturing method begins with a single functionalized fiber, or a fiber that has been chemically or physically modified to have specific properties, that serves as a versatile building block. The new 3D material composite will then be analyzed and implemented for a variety of structural functions.
If successful, the composite will extend the operational range of electric vehicles and achieve massless energy storage, resulting in weight reductions and enhanced energy efficiency.
The insights gained from this research will drive the advancement of next-generation lightweight materials, catering to the growing demand for EVs.
Dong’s work will also incorporate education and outreach activities.
“Throughout this project, I aim to motivate engineering students to pursue graduate study and broaden participation in clean energy manufacturing,” he says.
Beyond cars, this technology has the potential to transform complex systems including aircraft, spacecrafts and even ships. A deep understanding of this new manufacturing process has potential to create other multifunctional structural composites for applications such as sensing, health monitoring, energy harvesting and morphing — a process involving changing the shape of a structure to adapt to its surroundings.
“This project will advance the design and fabrication of next-generation lightweight multifunctional materials, paving the way for innovative approaches in the deployment and decentralization of high-performing energy storage units,” Dong says.
More Science and technology

Turning up the light: Plants, semiconductors and fuel production
What can plants and semiconductors teach us about fuel production?ASU's Gary Moore hopes to find out.With the aim of learning how to create viable alternatives to fossil-based fuels, Moore — an…

ASU technical innovation enables more reliable and less expensive electricity
Growing demand for electricity is pushing the energy sector to innovate faster and deploy more resources to keep the lights on and costs low. Clean energy is being pursued with greater fervor,…

What do a spacecraft, a skeleton and an asteroid have in common? This ASU professor
NASA’s Lucy spacecraft will probe an asteroid as it flys by it on Sunday — one with a connection to the mission name.The asteroid is named Donaldjohanson, after Donald Johanson, who founded Arizona…