Curbing concrete’s carbon emissions with innovations in cement manufacturing
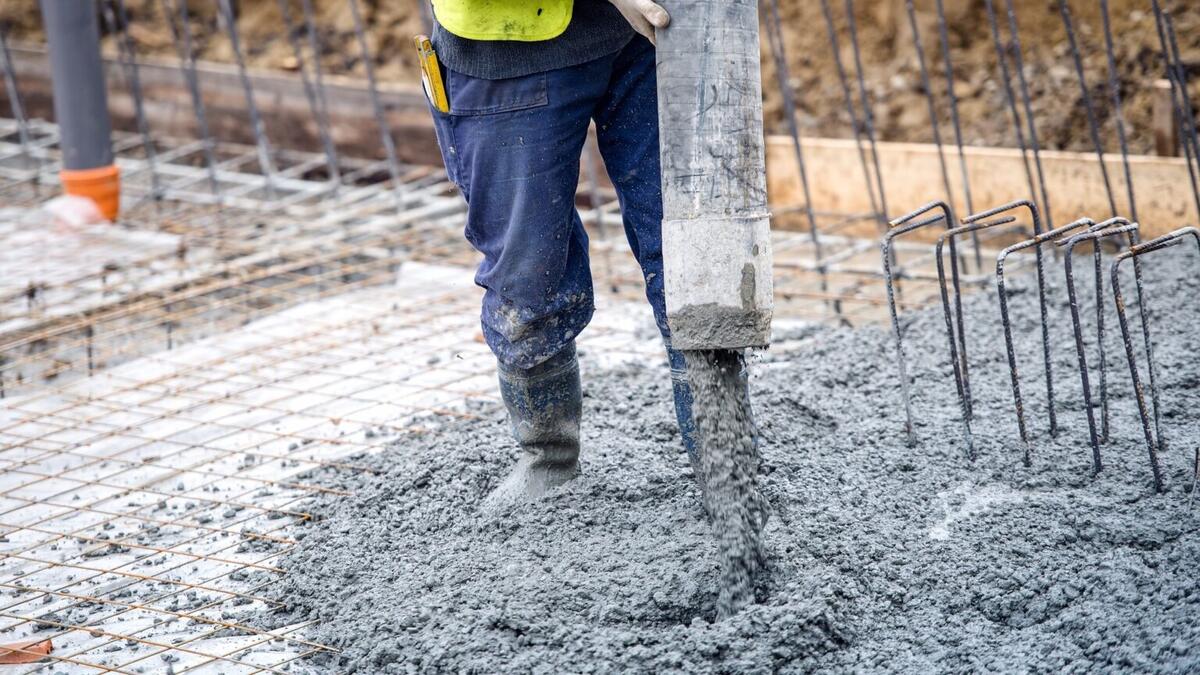
Concrete and cement manufacturing are among industrial processes producing large amounts of carbon dioxide emissions, contributing to air pollution, global warming and other threats to human and environmental health. Arizona State University researchers are engaged in research pursuits to find ways to significantly reduce those hazardous impacts. Image courtesy Ag Shotcreteservices/Pixabay
Concrete is second only to water as the most widely used material in the world, and cement is the essential “manufactured” ingredient in concrete. More than 30 billion tons of concrete are used every year, and the demand for it continues to rise significantly with increases in infrastructure construction projects.
The primary ingredient in cement manufacturing is limestone, which when heated to about 900 degrees Celsius converts to calcium oxide, resulting in the release of carbon dioxide, or CO2. The calcium oxide is then heated up to as much as 1,500 degrees Celsius with silica and alumina sources to produce the binding component of cement known as cement clinker.
In addition to the CO2 released from limestone, the use of fossil fuels to provide the high heat for the chemical conversion of calcium oxide results in substantial CO2 emissions. In total, one ton of cement typically produces about 0.8 to 0.9 tons of CO2 emissions, resulting in approximately 8% of the world’s anthropogenic CO2 emissions, and about 25% of all industry carbon emissions.
“If cement manufacturing were ranked with individual countries based on their carbon impacts, the cement industry would be the third largest CO2 emitter overall in the world after China and the United States,” says Narayanan Neithalath, the Fulton Professor of Structural Materials in the School of Sustainable Engineering and the Built Environment, part of the Ira A. Fulton Schools of Engineering at Arizona State University.
Through a National Science Foundation Future Manufacturing Research Grant, Neithalath and his research team are exploring new techniques for manufacturing cement to reduce carbon emissions through a synergy of novel energy sources and alterations in the processes and ingredients used.
“If we stand a reasonable chance of staying below the two degrees Celsius warming target set by the Paris Agreement, cement-related emissions will have to fall by more than 20% in the coming decade, after accounting for about a 20% increase in cement production and consumption to meet the demands of economic development and urbanization in many parts of the world,” Neithalath says.
Team of experts taking on big challenge
Cement manufacturing has come to be known as a particularly hard-to-decarbonize operation, largely because of CO2 emissions produced by the standard chemical process used by industry. Standing in the way of a solution is the lack of economical and scalable options to provide the high temperatures needed to produce the necessary chemical reactions required for the production process.
“Construction is a big contributor to climate change,” Neithalath says. “There is no other material that can do all that concrete can, and since the demand for the product is not going to change and the construction industry is very comfortable with Portland cement, we must look carefully at alternate processing options for cement, to control the carbon emissions.”
Portland cement is the type of cement most commonly used as a basic ingredient of concrete, as well as mortar, stucco and some types of grout.
Cement companies have done well over the past several decades to ensure their production plants are energy efficient, Neithalath says. But regardless of the energy source used, the carbon dioxide produced from calcium carbonate still has to go somewhere, he adds.
“Several research projects around the world are looking at multiple solutions to this vexing problem,” he says. “There is no one lever to reducing concrete’s carbon emissions, but there is a general consensus that process changes in cement manufacturing could have the highest impact, though that could be the hardest thing to do.”
The NSF Future Manufacturing Research Grant project brings together ASU researchers with expertise in a variety of fields, including Patrick Phelan, a professor in the School for Engineering of Matter, Transport and Energy, part of the Fulton Schools; Dong-Kyun Seo, a professor in the School of Molecular Sciences; and Diana Bowman, the associate dean for applied research and engagement in the Sandra Day O’Connor College of Law at ASU.
Other partners include Aditya Kumar, an associate professor of materials science and engineering at Missouri University of Science and Technology, and Srinivas Kilambi, a chemical engineer and innovator.
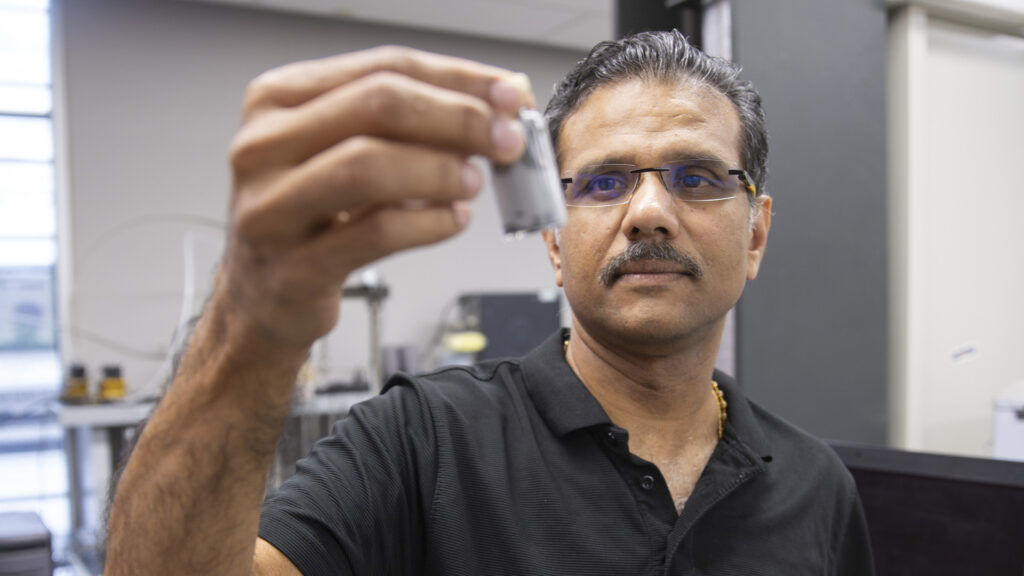
Professor Narayanan Neithalath’s work is contributing to the development of innovations to make concrete production eco-friendly, improve cement manufacturing and achieve advances in construction processes. Neithalath’s accomplishments to date have earned him the status of an American Concrete Institute Fellow. Photo by Bobbi Ramirez/ASU
Small changes can solve big problems
To address these carbon emission challenges, Neithalath says the research will focus on two main goals. The first involves separating lime from the limestone without producing carbon dioxide through novel electrolytic and hybrid routes. The second involves cement synthesis through a low-energy pathway, utilizing autocatalysis, a process for which energy can be provided through renewable sources such as solar power.
The important questions Neithalath and his research team will address relate to the consistency of cement produced and the scalability of the production process.
“While this is likely feasible experimentally, these are relevant questions when it comes to large-scale production and industry adoption of what we can develop,” Neithalath says.
There is a need to enable significant advancements by industry without requiring complete replacement of existing manufacturing infrastructure, he says, because the costs and time necessary to do that quickly would put big strains on businesses.
Manufacturing and building industries also want to retain the comfort associated with the use of traditional cement and concrete, especially their unique properties and the capability to manufacture concrete in the large volumes needed to do infrastructure development at manageable costs, which ensures manufacturing companies their products will be the materials of choice for construction.
“The big challenge is not only about creating a new manufacturing process that is environmentally sustainable,” Neithalath says. “It is also about manufacturing concrete with the lowest carbon emissions possible without a big increase in the price. This is what we hope to accomplish.”
Monica Williams contributed to this article.