ASU center helps Southwest manufacturers improve energy efficiency
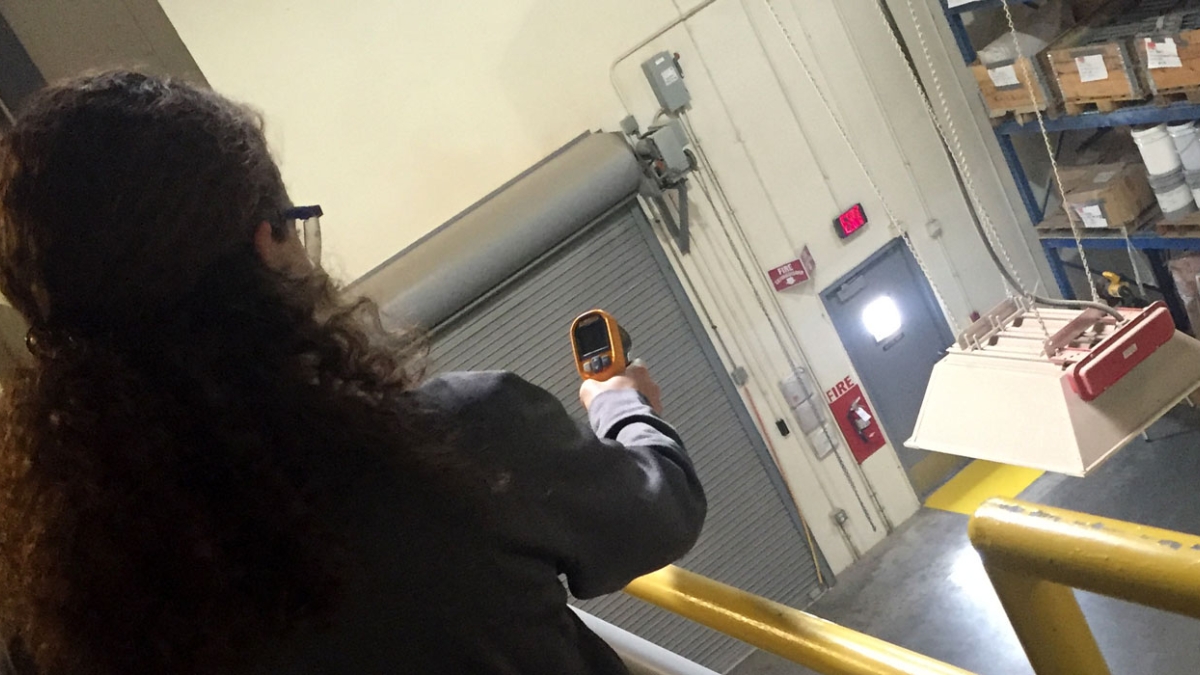
Arizona State University received $1.5 million over five years from the Department of Energy’s Office of Energy Efficiency and Renewable Energy to create an Industrial Assessment Center to help make the U.S. manufacturing industry more energy-efficient, productive and secure. Faculty and students from ASU’s Ira A. Fulton Schools of Engineering perform free site-specific, independent evaluations as part of this initiative, and students like manufacturing engineering undergraduate Kaitlin Kreck get hands-on experience performing industrial assessments. Photo courtesy of Sarah Johnston
In business, a better bottom line means better profitability, competitiveness and overall success. For energy-intensive businesses in the manufacturing sector, improving energy efficiency can reduce costs and send those savings straight to the bottom line.
The Department of Energy’s (DOE) Office of Energy Efficiency and Renewable Energy seeks to help make the U.S. manufacturing industry more energy-efficient, productive and secure through a nearly $35 million Industrial Assessment Centers (IACs) program.
IACs make site-specific recommendations to improve efficiency while providing undergraduate and graduate students the opportunity for firsthand exposure to industry manufacturing processes, energy assessment procedures and energy management systems.
Arizona State University is one of 28 universities the DOE tasked with establishing IACs in 2016. The DOE awarded ASU $1.5 million for the five-year project. The ASU IAC is led by faculty in the Ira A. Fulton Schools of Engineering: director and industrial engineering associate professor Rene Villalobos, assistant director and professor of mechanical and aerospace engineering Pat Phelan, and manager and assistant research technologist Jon Sherbeck.
Villalobos and Phelan — faculty members in the School of Computing, Informatics, and Decision Systems Engineering and the School for Engineering of Matter, Transport and Energy, two of the six Fulton Schools — bring their experience running an IAC at ASU for more than 15 years, a center that ended its work in 2006 after completing more than 400 assessments. Over the 40 years the DOE has funded the IAC program, centers have provided more than 17,000 assessments and more than 130,000 recommendations for improvement.
A large and growing manufacturing state
Arizona’s total manufacturing output in 2012, the most recent year for which data is available, was at the highest value ever recorded at $21.9 billion. Between 2009 and 2013, manufacturing exports increased by 25 percent, representing about 84,000 jobs.
The state’s top five manufacturing industries, ranked by their contributions to the state’s gross domestic product, are computer and electronic products, transportation equipment, food and beverage and tobacco products, miscellaneous products and chemicals, according to In Business Greater Phoenix magazine.
The ASU IAC serves an area beyond Arizona into southern Nevada/Las Vegas and western New Mexico, an area “which is not served by any other IAC,” Phelan said.
The area also represents the states with fast-growing populations relative to the country as a whole, driven in part by high job growth — Arizona was ranked eighth and Nevada sixth in 2014 by the U.S. Chamber of Commerce Foundation.
A mutually beneficial service
ASU’s IAC and the 27 others conduct free assessments for small manufacturers with fewer than 500 employees, gross annual sales below $100 million and energy bills between $100,000 and $2.5 million per year.
“ASU, as an independent and experienced third party, provides an unbiased assessment that plant managers can use to justify capital expenditures for energy-efficiency improvements, or to seek out specialists from the private sector to perform a more in-depth analysis,” Phelan said.
In addition to energy efficiency, the ASU IAC also assesses a manufacturer’s cybersecurity strengths and weaknesses, making recommendations on security measures such as using two-factor authentication to protect them against cyber attacks.
The IAC assessment team includes not only faculty members but students in undergraduate, master's and doctoral degree programs who help take measurements, come up with improvement ideas, and calculate cost savings.
During the one-day assessment visit, Sherbeck said the team looks for opportunities to improve energy efficiency as well as to reduce water consumption and waste streams.
“We look at their manufacturing processes and try to suggest productivity improvements, which might be how to track quality so you have fewer scrap parts, or how to arrange your processes so that there’s a minimum amount of travel of the hardware,” Sherbeck said.
It’s also a way for companies to get a fresh set of eyes on their operations and to break them out of the lull of “this is the way we’ve always done it,” Sherbeck said.
Sherbeck brings valuable experience to the team from his years of hands-on manufacturing experience, having put himself through university by working as a machinist and later full-time building all kinds of systems in industry.
After the assessment, the IAC team develops recommendations and delivers a confidential report to the client within 60 days.
“We attempt to determine how much cost the company can save, how much it’ll cost them to implement improvements and determine what the payback period would be,” Sherbeck said.
Six months after the assessment, the team conducts a follow-up visit and reports to the Department of Energy what improvements the company implemented.
In its first year, the ASU IAC plans to do 13 assessments, followed by 20 assessments in subsequent years.
The team has already started conducting assessments and is ramping up a marketing campaign to increase the manufacturing community’s awareness of these free services.
Community partners round out the team
The ASU team partners with other local organizations to identify potential clients and works with power companies to identify energy-efficiency improvement opportunities.
RevAZ, a business improvement and training organization that is part of the Arizona Commerce Authority, also helps identify potential clients for the ASU IAC.
Lincus Inc., a sustainability and efficiency evaluator, helps the ASU IAC with energy-saving alternative practices.
Outside Arizona, Nevada Industry Excellence helps with industrial business productivity and productivity recommendations.
Educating the next generation of engineers
Besides the costs of measurement equipment purchases and travel to and from industry clients, the nearly $1.5 million in funding supports student involvement in the program.
“These funds are used to support a large number of undergraduate and graduate students, mostly from engineering, who identify the clients, perform the assessments, develop the analysis and, finally, prepare and deliver the reports,” Phelan said.
Students involved get a “tremendous educational experience” where they can apply coursework to real manufacturing facilities, Phelan said, and soon they also will be able to participate in a new planned educational program in “clean-energy manufacturing.”
Both students and faculty get to learn what really matters to industry through the experience.
“Participating companies are helping ASU students and faculty become more knowledgeable about industrial practices and problems, which in turn helps make ASU’s engineering research and educational programs more relevant and impactful,” Phelan said.
Mechanical engineering doctoral candidate Nicholas Fette said his involvement in the ASU IAC has been a great learning experience. After a few months as student lead of the ASU IAC, he said he has a better understanding of manufacturing issues in Arizona in addition to better insight into how the university conducts business and the challenges of planning and communicating effectively with large organizations.
“Now having conducted a few site visits, I feel I have been exposed to many more aspects of this industry than were touched on in my academic training, and I’ve found some problems and unanswered questions worthy of research effort,” Fette said. “It has been a great experience, and I hope that we can develop more hands-on opportunities for students like this one.
Sherbeck notes that the experience will help lead to better-qualified graduates.
“The DOE considers that there are not enough qualified people to do this kind of [assessment] work,” Sherbeck said. “The program is intended to help small manufacturers, but it’s also intended to lead to more graduates capable of doing this kind of work.”
More Science and technology

Hack like you 'meme' it
What do pepperoni pizza, cat memes and an online dojo have in common?It turns out, these are all essential elements of a great…

ASU professor breeds new tomato variety, the 'Desert Dew'
In an era defined by climate volatility and resource scarcity, researchers are developing crops that can survive — and thrive —…

Science meets play: ASU researcher makes developmental science hands-on for families
On a Friday morning at the Edna Vihel Arts Center in Tempe, toddlers dip paint brushes into bright colors, decorating paper…