Innovative upcycling
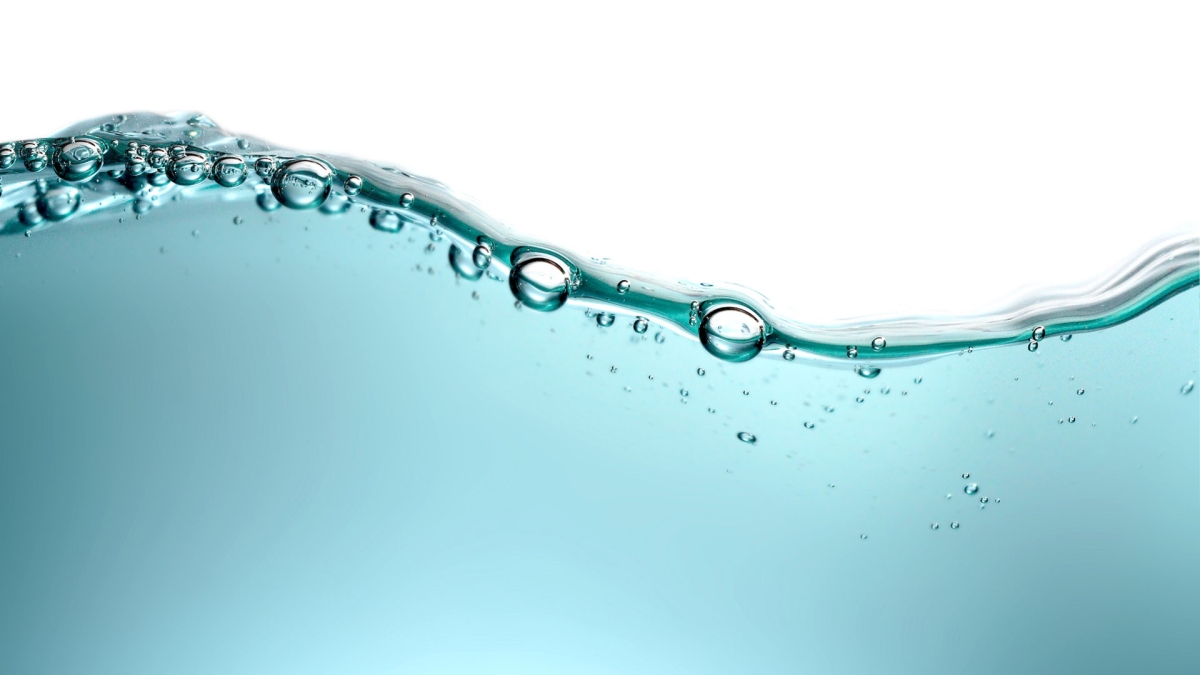
Clean water sources can become contaminated with nitrates from fertilizer-contaminated runoff and other industrial processes. Arizona State University researchers are collaborating on a multi-institute team to develop a new process to both decontaminate polluted water and generate valuable ammonia chemicals at the same time. Photo courtesy Shutterstock
Fertilizer and water are essential ingredients to support the farming that feeds more than 7.7 billion people on the planet. But while fertilizer is beneficial for growing food, nitrogen-based compounds called nitrates from fertilizer-contaminated runoff and other industrial processes can also pollute already scarce clean water sources.
We can’t live without water or fertilizer, so something must be done.
Christopher Muhich, an assistant professor of chemical engineering in the Ira A. Fulton Schools of Engineering at Arizona State University, is working with a multi-institute research team to develop a new process that can efficiently turn nitrate-contaminated wastewater and polluted groundwater into valuable ammonia and drinkable water.
“The generation of a useful product from waste, or upcycling, solves two problems at once: removing a toxin and generating a useful product with a lower energy input,” Muhich says.
The ammonia generated from this process can later be used to produce ammonium chloride, an important fertilizer, while the decontaminated water can be released into the ecosystem or further purified for municipal uses.
The results of this research — conducted with ASU, Rice University, Pacific Northwestern National Laboratory, Argonne National Laboratory, Oak Ridge National Laboratory and Canadian Light Source researchers and facilities — were recently published in the journal Nature Nanotechnology.
The challenging nature and critical role of ammonia
Ammonia is a versatile compound used in many substances, from fertilizer to fuels.
“Without exaggeration, ammonia production is the technology that supports the human population, as it is the precursor to fertilizer production,” Muhich says. “Without it, we would be unable to feed the world.”
However, current production methods used to meet the global demand of 150 million tons of ammonia per year require extensive infrastructure, use a high amount of energy and have a large carbon footprint.
Ammonia is made of one nitrogen atom and three hydrogen atoms, denoted by the chemical formula NH3. Using conventional processes, ammonia is a difficult chemical to produce because it requires converting nitrogen gas, a very stable molecule, into a high-energy ammonia molecule.
“Doing this requires high temperature, high pressure and currently the burning of methane to make hydrogen gas, or H2,” Muhich says. “Electrochemical routes are attractive because the hydrogen (atoms) can come from water,” lowering the carbon footprint of ammonia production.
An innovative approach to an old process
The electrochemical process, which involves passing an electrical current through a reaction cell to drive, or catalyze, chemical reactions, has been studied for the past 10 years as a more sustainable way to produce ammonia.
However, scientists haven’t been able to use electrochemical methods to create ammonia at the production rates and quality necessary to be useful, especially from industrial wastewater sources, which have relatively low nitrate concentrations.
In addition, generating ammonia from nitrate-contaminated water is difficult for many reasons. The reaction between nitrogen, oxygen and hydrogen in the contaminated water can lead to undesired effects, such as a side reaction to produce hydrogen gas, which wastes the energy needed to fuel the electrochemical process’s chemical reaction, or the creation of other compounds that are even more toxic than nitrates.
To selectively achieve efficient ammonia production through an electrochemical process, Muhich and the research team developed a new catalyst using an innovative approach: dispersing ruthenium atoms into a copper nanowire matrix, which the team calls Ru-CuNW. This single-atom approach of integrating ruthenium into the matrix has not been explored by other research teams before.
A power couple that gets results
Ruthenium and copper create a powerful combination for electrochemical reactions. Ruthenium improves performance to 99% nitrate ion conversion into ammonia while copper suppresses the “parasitic side reactions” that generate hydrogen gas instead of ammonia.
The finding that hydrogen gas production is suppressed with the ruthenium-dispersed copper nanowire catalyst is the team’s most important development, Muhich says.
“This is one of the key reasons electrochemical nitrate reduction has failed, because you don’t want to use expensive electrons for a side reaction,” he says.
This process also shrinks the infrastructure, energy and carbon footprint of the ammonia production because it works in ambient temperature and pressure.
Support from a multi-institutional research team
The research team included two of the institutions that make up the Nanosystems Engineering Research Center for Nanotechnology Enabled Water Treatment, or NEWT Center. Hosted at Rice University in Houston, the center also includes researchers from ASU, the University of Texas at El Paso and Yale University, in addition to industry and government partners.
In developing the ruthenium-dispersed copper nanowire catalyst technology, ASU researchers worked on understanding what was happening at the molecular level during the electrochemical process.
“We did the quantum calculations to understand why these catalysts were so good, and what the process looks like at the atomic scale,” Muhich says. “We modeled the individual chemical reactions along the path.”
The Rice University team performed testing and characterization experiments and analysis along with researchers from the national laboratories and Canadian Light Source.
Future work for the team includes translating the ruthenium-dispersed copper nanowire catalyst’s performance into large-scale systems and working to reduce the amount of ruthenium and other expensive platinum group metals used in the catalysts.
More Science and technology

Cracking the code of online computer science clubs
Experts believe that involvement in college clubs and organizations increases student retention and helps learners build valuable…
Consortium for Science, Policy & Outcomes celebrates 25 years
For Arizona State University's Consortium for Science, Policy & Outcomes (CSPO), recognizing the past is just as important as…
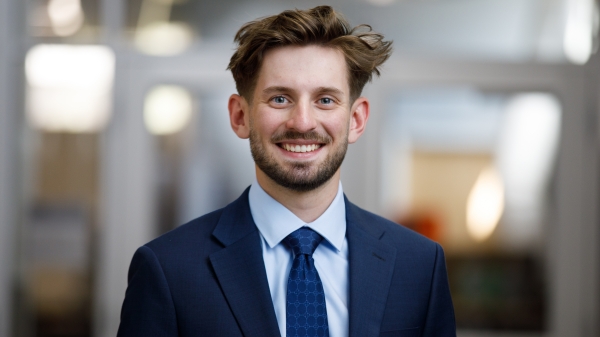
Hacking satellites to fix our oceans and shoot for the stars
By Preesha KumarFrom memory foam mattresses to the camera and GPS navigation on our phones, technology that was developed for…