ASU project explores 3-D printing frontier
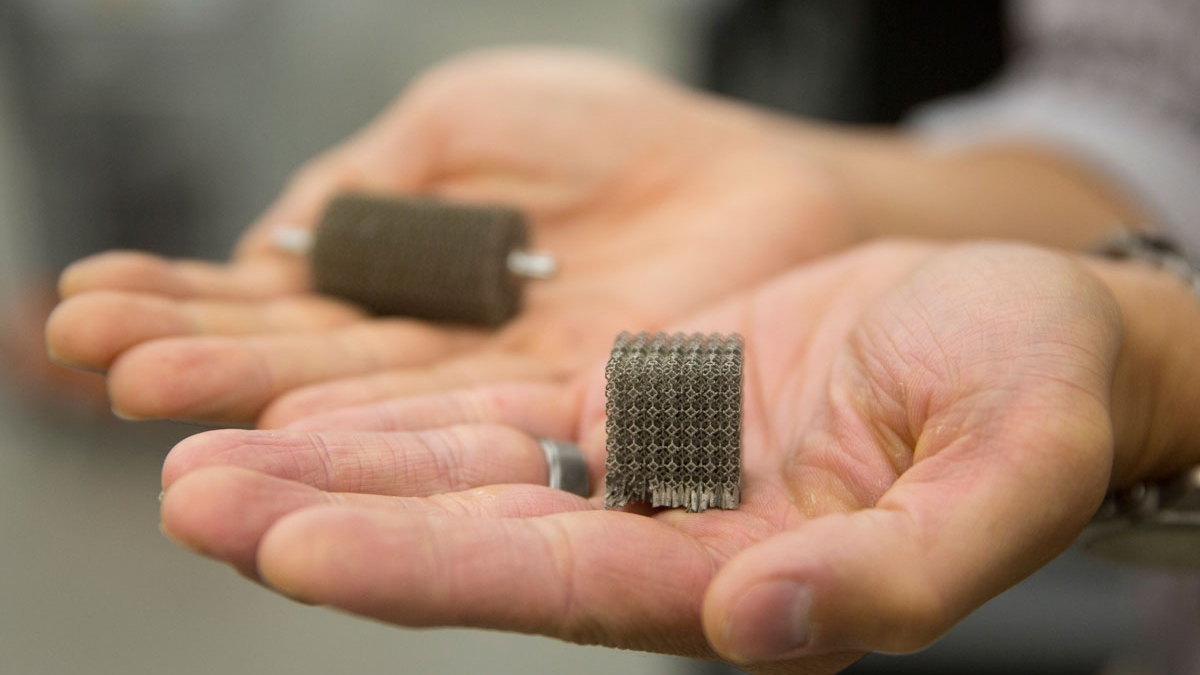
Lattice structures are a promising area of additive manufacturing, or 3-D printing. These designs have cost and performance advantages over solid structures, but the ability to control their mechanical, thermal, and acoustical behaviors is only now being explored by an ASU researcher and his industry partners. Photo by: Pete Zrioka/ASU
In the year of Star Trek’s 50th anniversary, the reality of 3-D printing, or additive manufacturing, is advancing closer to the series’ fictional replicator technology — the final frontier of manufacturing.
Researchers from Arizona State University’s Ira A. Fulton Schools of Engineering and its industry partners are boldly going where no researcher has gone before in the study of lattice structures in additive manufacturing.
Lattice structure design and manufacturing is one of the most promising areas of additive manufacturing research today. It capitalizes on the unique advantage of additive manufacturing processes: complexity for free. Though latticed designs are more complex than solid ones, they do not cost more to produce when additive manufacturing processes are used. Systematically and methodically removing material in the design can lower material costs, increase design flexibility and functionality and reduce weight without negatively affecting mechanical performance or production time and cost.
These materials are used in an increasing number of applications, especially in components where strength-to-weight ratio is critical. Beyond mechanical advantages, lattice structures can also be designed and tuned to having engineered thermal properties for conductors or insulators, acoustic properties for sound cloaking, and even optical properties for visual cloaking.
While optimization efforts are ongoing in this area of additive manufacturing, unaddressed is the issue of modeling the behavior of 3-D printed lattice structures.
“By understanding the fundamental physical principles that govern the correlation between the manufacturing processes and the behaviors of lattice structures, we can advance toward better lattices and better processes to build them,” said Keng Hsu, assistant professor of manufacturing engineering.
Hsu creates more, new capable additive manufacturing processes and additively manufactured materials as part of his Advanced Multi-scale Manufacturing Lab. His research is focused on the creation and evolution of manufacturing processes and materials by studying and applying the fundamental principles of material science and material-energy interaction. This has led to breakthroughs such as being able to 3-D print solid metals at room temperature.
Bridging theory and reality is what keeps Hsu interested in the field of advanced manufacturing and materials. In practice, this means creating processes through which theoretical concepts can be produced in real life, specifically new manufacturing processes and materials.
Hsu is working with Phoenix Analysis & Design Technologies, Honeywell Aerospace, LAI International and Professor Howard Kuhn of the University of Pittsburgh to develop physics-based, geometry-independent models that describe material behavior and strength of complex lattice structures in order to increase performance and reduce the amount of material needed. They specifically explore three additive manufacturing processes — fused deposition modeling, laser-bed powder bed fusion and electron beam melting — with thermoplastic and metal materials.
The team’s efforts related to their project, “A Non-Empirical Predictive Model for Additively Manufactured Lattice Structures,” earned them a place among seven teams selected to be part of an $11 million grant from the National Additive Manufacturing Group, America Makes. Hsu and the team were awarded $281,000 over a period of 18 months.
The America Makes Distinguished Collaborator Award recognizes individuals or organizations with exceptional commitment and dedication to the innovation of additive manufacturing technology and practices. The award honors these individuals and organizations for cultivating collaborations between academia, government and industry.
“[The award] marks a very important start of a collaboration between PADT and ASU in the additive manufacturing research space,” said Hsu, the co-principal investigator on the project. PADT Senior Technologist Dhruv Bhate is author and principal investigator of the project proposal.
It also puts Arizona on the map for 3-D printing advancements in academia and industry.
ASU’s Polytechnic campus is home to the Additive Manufacturing Center, a 15,000-square-foot additive manufacturing facility with $2 million of state-of-the-art 3-D printing equipment — which uses plastics, polymers, metals and composites in five different additive manufacturing processes — in addition to a range of materials processing and analytical tools.
Another part of the team’s proposal is an online, collaborative additive manufacturing textbook for comprehensive information. It’s designed as a “living” textbook, which is important to keep up-to-date in a field where more than 50 papers are published worldwide every day, according to PADT.
While we’re still far from the replicator’s capabilities of creating complete physical things out of pure energy, Hsu and his Fulton Schools team and industry partners have a strong platform from which they can work together to solve bigger science and engineering problems in additive manufacturing.
“Let the exciting research work begin!” Hsu said.
More Science and technology

Cracking the code of online computer science clubs
Experts believe that involvement in college clubs and organizations increases student retention and helps learners build valuable…
Consortium for Science, Policy & Outcomes celebrates 25 years
For Arizona State University's Consortium for Science, Policy & Outcomes (CSPO), recognizing the past is just as important as…
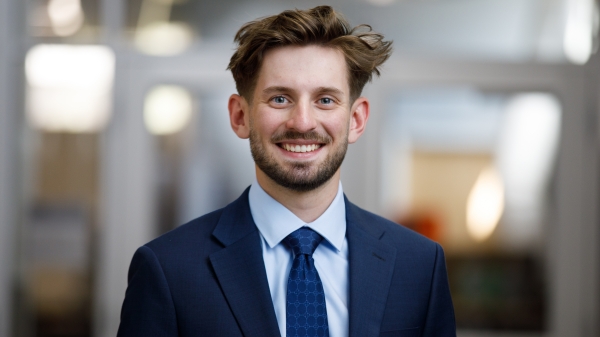
Hacking satellites to fix our oceans and shoot for the stars
By Preesha KumarFrom memory foam mattresses to the camera and GPS navigation on our phones, technology that was developed for…