As an example of an engineering breakthrough, the tiny metal arch Owen Hildreth keeps in his office at Arizona State University isn’t anywhere close to visually impressive. But it is something special once you understand how it was made.
It represents potentially game-changing progress in the emerging realms of 3-D printing and additive manufacturing — an advance that could have a dramatic impact on how things are made from metals.
Hildreth, an assistant professor of mechanical and aerospace engineering in ASU’s Ira A. Fulton Schools of Engineering, has collaborated with several colleagues to develop a technique that promises to make manufacturing of metal components, devices and structures less expensive, technically complex and labor intensive.
Significantly, the process overcomes what has been a nagging difficulty for the 3-D printing of metal objects.
Alternative to laborious machining processes
3-D printing has been a major driver of additive manufacturing. Conventional manufacturing is essentially a subtractive process. Manufacturers start with a mass of material and remove — or subtract — parts of the mass to produce a desired object.
“It’s like sculptors working with blocks of marble,” Hildreth explained. “They remove parts of the marble blocks until they get the shape of whatever kind of sculpture they wanted to create.”
Additive manufacturing, particularly with the use of 3-D printing technology, is the opposite, he said: “You just add layers of material until you get what you want. You extrude products. The printer just pushes things out in one piece.”
The process works great with lightweight and flexible plastics and polymers. But with weighty metals, it’s much more of a challenge.
That’s because when objects made of plastics and similarly “soft” materials emerge from a 3-D printer with extraneous material, the unneeded material can usually be easily cut away to give the object its intended form.
With metals, however, the high temperatures required to print them cause objects to warp as they are being printed, and so the process requires metal supports strong enough to prevent this warping. After printing, the supports must be removed to produce an object with its intended shape.
The only way to remove such supports has been through heavy-duty, laborious and painstaking machining techniques, involving the use of computer numerical control milling machines and wire electrical discharge machining.
Electrochemical etching and chemical baths
Even when 3-D printing of plastic and polymer materials does require supports, “it’s easy to make them go away,” Hildreth said. “You just break them off, or you melt them off with a soldering iron. Or better yet, you print supports made out of a water-soluble material. You can just dunk your object in water for an hour and the support material is gone.”
That doesn’t work in printing metal objects because they require metal supports during the printing process — and metals are not water-soluble.
But here is where the new technique demonstrated in the making of Hildreth’s tiny metal arch comes into play.
Combining his expertise with that of his collaborators, they employed a printing method — called directed energy deposition — that enables the printing of an object using two kinds of metal at the same time in combination, and then electively dissolving the “sacrificial” material with a simple electrochemical etching technique.
To demonstrate their new approach, they printed the stainless steel arch supported by carbon steel.
“The stainless steel is very chemically resistant. The carbon steel is not very chemically resistant,” Hildreth said.
The printed metal structure was immersed in a “chemical bath” of nitric oxide and bubbling oxygen capable of dissolving metals that are not chemically stable — in this case, the carbon steel supporting the top of the arch.
Arizona State University engineer Owen Hildreth (right, with ASU engineering graduate student Avinash Mamidanna) is part of a team that has developed a technique to enable more efficient and less costly manufacturing of 3-D-printed metal materials. Photo by Jessica Hochreiter/ASU
Combining team's wide range of expertise
“We took advantage of the differences in the chemical and electrochemical stability between the two metals,” Hildreth said. “The carbon steel was etched away without any machining. The stainless steel wasn’t affected. So what we have is the world’s first 3-D-printed metal arch made with directed energy deposition.”
What that makes possible is a big reduction in the amount of post-processing required to remove support structures from 3-D-printed metal components.
“We’re fairly certain our method is going to be applicable to a broad range of metals used in manufacturing,” Hildreth said.
To achieve the advance, Hildreth teamed up with Timothy Simpson, a professor of mechanical and nuclear engineering as well as industrial and manufacturing engineering at Pennsylvania State University, and a leading expert in both 3-D printing of metals and additive manufacturing.
They were joined by Pennsylvania State University engineering research associate Abdalla Nassar and Kevin Chasse, a corrosion engineer with the Naval Surface Warfare Center.
Together they authored the report “Dissolvable Metal Supports for 3D Direct Metal Printing” published in a recent edition of the research journal 3-D Printing and Additive Manufacturing that attracted immediate attention from manufacturing industry news outlets.
Mapping steps to further engineering advances
The team is already at work refining their techniques and mapping the next step forward. They hope to help develop methods that would apply the capabilities of 3-D printing to manufacturing metal products and structures to further eliminate the need for multiple parts and multiple assembly steps.
Along with private industry, they see the Department of Defense and NASA being particularly interested in supporting their endeavors.
They have also submitted a proposal to the National Science Foundation for support of research to look more deeply at the fundamental physics and chemistry involved in 3-D printing and additive manufacturing.
“We want to see what we can learn from mixing different materials together and printing them on top of each other,” Hildreth said. “We want to more closely study the diffusion and corrosion mechanisms involved in manipulating metals, with a focus on stainless steel, aluminum, titanium and an iron-nickel-chrome alloy.”
Local support put research on fast track
Hildreth’s recent research in these areas has been funded in large part through a Bisgrove Scholars Program award he received in 2015 from Science Foundation Arizona.
Bisgrove Scholars awards are given to academics and researchers whose work is deemed to have “the potential to transform ideas into great value for society.”
Hildreth said the support “gave me the freedom to pursue this work, which so far has led to seven patent applications and the development of two startup companies.”
Top photo: The making of this small metal arch involved a novel technique that promises to make it easier to produce metal objects using 3-D printing. The arch was formed by first printing a stainless steel arch supported in the center by carbon steel. After printing, the carbon steel was electrochemically removed in a mixture of nitric acid with bubbling oxygen. Since carbon steel is easily dissolved while stainless steel isn’t, this simple process leaves behind a free-standing stainless steel arch that didn’t require any of the expensive machining operations that typically plague 3-D metals printing. This process is expected to dramatically simplify 3-D metals printing. Photo courtesy of Owen Hildreth
More Science and technology

Cracking the code of online computer science clubs
Experts believe that involvement in college clubs and organizations increases student retention and helps learners build valuable social relationships. There are tons of such clubs on ASU's campuses…
Consortium for Science, Policy & Outcomes celebrates 25 years
For Arizona State University's Consortium for Science, Policy & Outcomes (CSPO), recognizing the past is just as important as designing the future. The consortium marked 25 years in Washington, D…
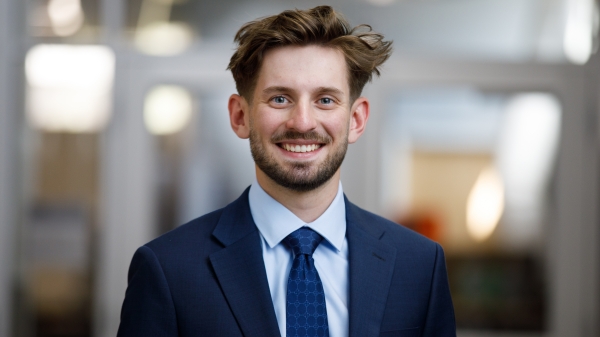
Hacking satellites to fix our oceans and shoot for the stars
By Preesha KumarFrom memory foam mattresses to the camera and GPS navigation on our phones, technology that was developed for space applications enhances our everyday lives on Earth. In fact, Chris…