Keeping the Navy’s aircraft in shipshape
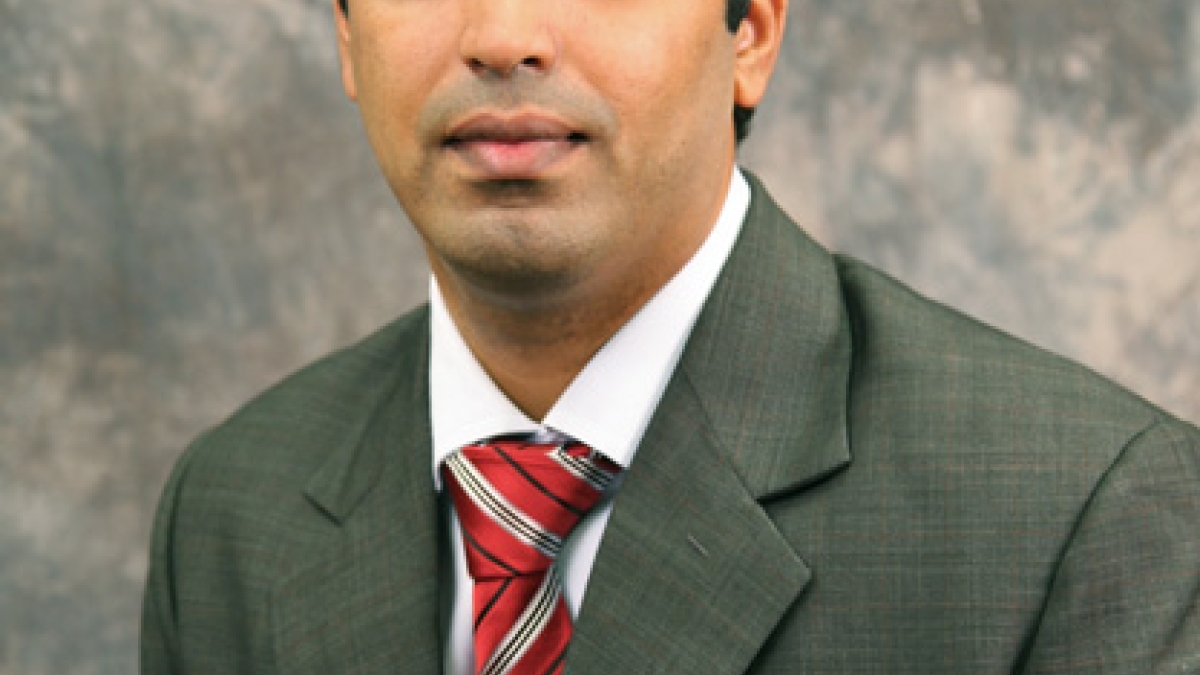
Associate professor Kiran Solanki is conducting breakthrough research with support from the Office of Naval Research and his team at ASU.
Engineers at Arizona State University are tackling research to aid the performance and safety of the U.S. Navy’s aging fleets.
Service loads paired with harsh environmental conditions are of paramount concern to naval officials as they seek to predict the lifetime of maritime structures, primarily aircraft, essential for national security and mission readiness.
As the Navy primarily operates in harsh saline environments, corrosion has a significant influence on the materials that make up naval aircraft.
Corrosion is not only a big word in regards to structural integrity, it is also an expensive word for the Navy.
For instance, according to a Logistics Management Institute study for the Department of Defense, the cost of corrosion for Navy and Marine Corps ships and aviation between 2010 and 2012 was a combined $5.7 billion. Corrosion accounted for 29 percent of the Navy and Marine Corps aviation maintenance cost during those years.
The study also predicted that the Navy experiences, on average, 20 percent down time due to unscheduled maintenance every year.
However, associate professor Kiran Solanki and his collaborators champion an approach that doesn’t look at corrosion in isolation.
Supported by a $635,000 grant from the Office of Naval Research, Solanki’s team is developing a more complete method to study joint degradation behavior by combining electrochemical and material/mechanical concepts.
He points out a problem encountered in the field that the scientists and engineers who build long-lasting naval structures do not collaborate enough. Electrochemists study the effects of corrosion. Materials scientists study the microstructural influence of fatigue and fracture. The problem is they don’t look at how these areas impact each other.
“When you have material deformation, such as during fatigue, and corrosion happening simultaneously in structural materials you have the worst case scenario,” said Solanki, the grant’s principal investigator. “Our goal is to combine the knowledge of these two areas and to look at how they influence each other.”
Nik Chawla, a Fulton professor of materials science and engineering at ASU, is the co-principal investigator of the grant, and offers expertise in material microstructural influence on the fatigue behavior.
In particular, Solanki and Chawla aim to uncover the precise crack growth-driving mechanisms that occur when naval-relevant materials experience mechanical load in a saline environment.
Loading can take on many forms, but Solanki looks specifically at environmental and mechanical load — and most importantly how they operate together. Environmental load refers to corrosion that occurs in the maritime environment. Mechanical load refers to structural loads.
According to a recent study published in Corrosion Reviews, more than 80 percent of structural failures in Navy ships and aircraft were due to the combined effects of environmental and mechanical loading.
Solanki aims to develop a predictive framework to improve the accuracy of structural prognosis.
“Understanding the combined effects environmental and mechanical loads have on the primary materials used in military aircraft and sea craft, in addition to improving upon predictive capability, will undoubtedly improve mission readiness,” said Solanki.
Solanki and Chawla are also advancing this effort with another ONR grant totaling more than $506,000. Chawla is the principal investigator of this Defense University Research Instrumentation Program (DURIP) grant, and Solanki the co-principal investigator.
Solanki describes their approach as seeking a bottom-up understanding, meaning they’re studying electrochemical and structural problems at a very small scale to better understand problems that happen at a larger, more visible layer. A lot is happening at the nano-scale level before a crack visually appears in the materials that make up marine aircraft, for example.
“We are looking at features that are very, very small, but provide a critical understanding of structural integrity,” said Solanki.
Looking at the microstructural level, this research involves small-scale X-ray tomography experiments to get a microscopic view of the material’s behavior when experiencing damage. This method then yields information on which to base mathematical predictions of when and where materials will incur damage under varying conditions.
To Solanki’s knowledge there are no prior experimental-modeling studies looking at the combined effects of environmental and mechanical loading in naval structural elements — making this research the first of its kind.
“There’s a lot of history in the literature where they are looking at one of these aspects, but they’ve never pulled them together in the way we are,” said Solanki.
Building on previous research
In December 2015, Solanki wrapped up an ONR-funded effort, totaling more than $535,000, focused on mapping the role of environmental effects, such as corrosion, on the crack-tip stress field in naval structures.
Stress corrosion cracking is a leading cause of damage in structural components during naval service. Recurring and static mechanical loads result in damage near highly stressed areas. This damage manifests itself in the form of small surface cracks that can eventually result in catastrophic failure if undetected.
Solanki’s research under this grant aimed to sort out the stages of this stress-damage to help track structural degradation more reliably.
Following the bottom-up approach, he studied corrosion on a very small-scale. His team discovered that the presence of hydrogen enhances brittle behavior in iron, which accelerates stress-corrosion cracking.
He says this previous research effort helped him to gain a fundamental mechanistic understanding that will aid him as he seeks to combine his mechanical understanding with electrochemistry.
“The bottom-up approach helped us to move forward with our new grant focused on combined loading,” said Solanki.
The grant resulted in 11 publications, including in journals such as Acta Materialia, Scientific Reports and Royal Society Proceeding A. It also helped advance the research of two graduated doctoral students.
After successfully concluding this ONR-funded research, Solanki said he’s particularly excited about his latest grants because they promise “breakthrough results in corrosion and stress corrosion cracking, and doing things for the first time.”
More Science and technology
Extreme HGTV: Students to learn how to design habitats for living, working in space
Architecture students at Arizona State University already learn how to design spaces for many kinds of environments, and now they…
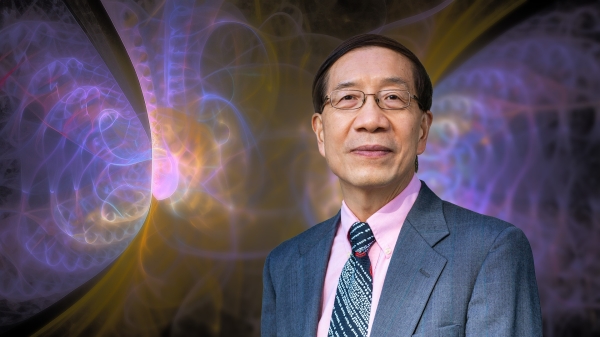
Human brains teach AI new skills
Artificial intelligence, or AI, is rapidly advancing, but it hasn’t yet outpaced human intelligence. Our brains’ capacity for…

Doctoral students cruise into roles as computer engineering innovators
Raha Moraffah is grateful for her experiences as a doctoral student in the School of Computing and Augmented Intelligence, part…